Master Woodworking: A Beginner's Guide to Mastering Woodworking and Woodcraft
Author: Andy Bowman
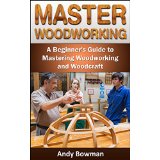
Book Series: Mens Hobbies
Introduction
Woodworking is an activity that involves either building or creating objects from wood. While many people may think of the same few items when they think of wood, the range of objects you can make with this material is quite tremendous. You can create an item as small as a key chain or as large as a gazebo. You can craft nearly anything you can imagine when you have the skill of woodworking at your disposal.
In addition, working with wood can be beneficial in a number of ways. These benefits are both physical and mental in nature, and shouldn't be discounted. Many people have been able to build a better life thanks to the power of woodworking.
It's easy to forget how physical of an activity woodworking is. It requires you to work carefully with your hands, but it also requires you to carry around large pieces of wood. A lengthy woodworking session can raise your heart rate and provide your body with a good workout. It's a great way to get into shape.
However, woodworking can be done even if you're not in peak physical condition. For example, many people afflicted by arthritis still enjoy this rewarding hobby. Wood crafting can be done from a wheelchair, and can still be done when you're feeling poorly. You just have to find the right project for your needs.
Engaging in a physical leisure activity like woodworking for at least 20 minutes a week can reduce your susceptibility to fatigue. It can also lower blood pressure and improve the body's overall function. Wood crafting is an excellent way to improve health. In fact, many doctors recommend that patients take on a hobby like woodworking.
Woodworking has a number of emotional benefits as well. Studies have shown that regular woodworking can significantly reduce the amount of stress in someone's life. It provides people with a sense of fun and freedom that can reduce the weight of the pressures in their lives. It can also help fight off depression, and can even ease depression symptoms.
Hobbies like woodworking also stimulate the brain, which can help stave off the natural decline in brainpower that comes with aging. A simple crafting project can help you to keep your mind sharp, and can help you to fight off cognitive decline. A challenging woodworking project is like a mental exercise.
Woodworking also allows you to strengthen relationships with your loved ones. Taking on a project with a family member can help you to build a deep bond with each other, and will allow you to build a number of lasting memories together. You can work on projects with your friends, your significant other, or even your children.
Children can be allowed in a woodworking area as early as age 4. From there, they can learn how to use tools safely, and can eventually begin taking on their own projects with minimal assistance. Woodworking with children gives them skills that will last them a lifetime, and can also aid in their development.
Woodworking can improve dexterity and fine motor skills, can teach a child how to solve problems, and can increase their hand/eye coordination. It can also build a child's self-esteem and increase their sense of independence. The more a family takes on woodworking projects together, the more benefits they'll see.
In addition to the above benefits, woodworking can save you a great deal of money. Wooden objects and furniture are extremely expensive if you buy them new, but wood crafting gives you the tools to make these things on your own. As your skills improve, the range of things you can make will increase.
While you may not be able to make a gazebo today, even the simple items you can make as a beginner will be quite useful. The projects found in this book are items any household can use, and can be created from small and inexpensive cuts of wood.
Wood is a renewable resource, which means that building objects from wood can also have a positive impact on the environment. Wood can store carbon, and can reduce carbon emissions released into the atmosphere. It's also a durable, strong material that will really last. Nothing about wood is disposable.
Anyone can benefit from making woodworking a part of his or her lives. The more time you spend working with wood, the more positive changes you'll see. Now is the perfect time to incorporate this wonderful hobby into your life. No one should wait to take advantage of all that woodworking has to offer.
What You Need to Get Started
If you're brand new to woodworking, getting started can seem overwhelming. There are tools to buy, skills to learn, and safety hazards to avoid. However, while woodworking is difficult to master, getting started is much easier than it may seem.
Your first step should be setting up a workshop. You'll want to find a place that has enough open space for you to work, and that is isolated from the rest of your home. You don't want anyone accidentally approaching you while you're working with dangerous tools.
Many people opt to set up their workshop in either their garage or their basement. Outdoor sheds can also be a great place for a woodworking station. However, even if you don't have extra space, you can still make room for a small workshop. Find ways to make efficient use of the space you do have.
For example, a portable table saw takes up minimal space, and can easily be stored if needed. A work stand is a good alternative to a larger worktable. A small filtration system will provide you with the ventilation that you need, and a saw hood can help control dust. There are a number of space-saving solutions available if you're willing to look for them.
Although the expense of setting up a woodworking shop can be daunting, it's not necessary to buy everything at once. A worktable or work stand and some essential power tools are all you really need to take on most beginning projects. You can always purchase additional tools, as you need them.
One of the most important things a woodworker can have is a circular saw. It can be used as a substitute for a table saw, and will allow you to make all kinds of cuts. Look for a saw that has high horsepower for its size and a safety switch.
A power drill is another vital tool. While corded drills offer more convenience, a power drill has more power and versatility. They allow you to take on a number of tasks without damaging your drill's battery. Look for a variable speed drill that has a wide range of features.
If you want to cut curved or circular patterns, you're going to need a jigsaw. A jigsaw is easy for a beginner to use, and is more versatile than you might think. Try to find a saw that feels comfortable in your hand when you hold it. A simple blade changing system is also important.
You'll need a sander, and there are a number of good options in this area. Your best would be a palm sander, which is easy to use and inexpensive, or a random orbital sander, which will give you a cleaner finish. Compare products available and decide which would be the best fit for you.
A quality router is something every woodworker can get use out of. The range of shapes they can place onto edges is quite impressive. A model with a stationary base will allow you to carry out a number of tasks, and can be mounted onto a table later on if you desire.
While a circular saw can carry out many of the tasks a table saw can, any woodworker will eventually need a table saw for their shop. It's a tool you'll find yourself using constantly on all kinds of projects. It also makes a great centerpiece for your shop.
In addition to stocking up on power tools, you'll want to pick up some hand tools. If you don't have them already, you'll need a claw hammer, a tape measure, a utility knife, a few chisels, and a screwdriver. You'll also want to have a layout square, a sliding bevel, and a block plane.
As you set up your workshop, you'll want to think about how you want your tools to be stored. A cabinet works very well for storage, but a simple shelving system can work just as well. It's important that every tool in your workshop has a proper place.
As your skills develop, there are a number of additional tools you'll want to acquire. It's likely that you'll need a drill press and several other types of saws, such as a band saw and a radial arm saw. You'll also want a jointer and a surface planer.
You should keep in mind that you don't need to buy all these products at once. It's best to slowly build up your workshop over time. As you spend more time on projects, you'll become more familiar with tools, and will have a better understanding of what to look for in your purchases.
Woodworking is a hobby that you'll be able to enjoy for the rest of your life. You don't have to rush to get the perfect workshop put together. You'll be able to do it little by little.
Selecting the Right Saw Blades
Even if the woodworking tools you own are top of the line, they're never better than the quality of their blades. No matter what type of saw you're using, a good blade will make it faster, easier, and safer. When a saw blade is in good condition, it'll also allow you to make cleaner cuts, which means you'll need to do far less sanding afterwards.
When you look for saw blades, you'll want to make sure that they're sharp enough to cut cleanly through your wood without causing damage. You'll also want to make sure they're the appropriate type of blade for your tool.
When you're looking at blades for a circular saw, you'll have two primary options. There will be rip blades and there will be crosscut blades. However, there are also combination blades that combine the properties of both blades.
A rip blade works by cutting with the wood's grain. Its teeth are very deep, but are limited in number. This helps clear away material after wood is cut. This type of blade is great for quick cuts, but doesn't leave a very clean finish.
In contrast, crosscut blades can provide an excellent finish. These blades cut with kerf, meaning slightly wider than the edge of the blade, using either carbides or chisel. With every other tooth, they alternate between cutting wide light or wide left. This means that it can take slightly longer to get a good cut.
As mentioned above, combination blades combine the features of both blade types, which often makes them an ideal choice. These blades have a wide variety of tooth-counts, generally ranging from about 24 tooth to 80 tooth. Blades with a high tooth count will cut more slowly, but provide a finer finish. Blades with a lower tooth count will cut aggressively, but leave a sloppier finish.
In addition to the blade types mentioned above, there are also specialty blades. These blades are usually designed with specific, non-wood materials in mind, and don't play a role in woodworking. However, there's one type of blade that many woodworkers may find quite useful: the dado blade. This type of blade can be used on either a table saw or a radial saw arm.
Dado blades are known for their ability to consistently achieve near-perfect results. These blades have a high number of teeth, and are able to achieve a special style of cut. The cut makes a wide groove in one piece of wood and then joins that groove with another piece. This achieves a smooth, even finish while still cutting quickly.
There are two types of dado blades. There's a stacked dado set, which provides a set of both inside and outside blades. This set also includes chippers and shims, which can be used to adjust the cutting width to your precise specifications.
There are also wobble blades. Rather than the traditional type of spin you see from a saw blade, these blades live up to their name and wobble back and forth. While the cuts these blades achieve aren't quite as precise as the ones that can be made by a stacked dado set, they can cut very quickly.
The right size blade for your saw will depend on the model of saw you use. Take the time to read through your saw's documentation before purchasing any new blades. This will ensure that whatever blade you do buy will work perfectly with what you have.
Over time, your saw blade will see a decrease in quality. It may become caked with pitch, or may simply become dull. All of these things can make the blade far less effective. Thankfully, there are solutions to all of these problems.
Your blades can be cleaned using a pitch cleaning solution purchased from your local home improvement store, or can be cleaned using a different method. Oven cleaner is an excellent way to get rid of pitch, and can save you money if you already have some in the house.
Alternatively, you could soak your blades in mineral spirits or kerosene overnight. In the morning, scrub them clean with a non-abrasive cleaning pad. Be sure not to use anything abrasive on your blades, and be sure to keep them far from any sources of flame while they soak.
If you need your blades sharpened, it's best to go to a professional. As long as your blades are of a high quality, a professional will be able to sharpen them a number of times. While inexpensive blades may be cheaper upfront, quality blades will wind up saving you money over time.
The blade is the most important part of any saw. When purchasing tools, make quality blades your top priority. You can often save money by purchasing a cheaper saw and then outfitting it with more expensive blades.
The right blades will make your woodworking projects easier, and will make the time you spend in your shop far safer. Take the time to find blades that are right for your saws, and be sure to keep those blades in good condition.
Safety in the Workshop
Although woodworking is very rewarding, the tools you use can be sharp and unforgiving. It's important to take every precaution to ensure you avoid injury while in your workshop. Taking basic safety measures will make your time in your shop far more enjoyable.
The most important rule you can follow is to wear safety gear at all times. You'll never know when you need the protection of goggles or a pair of gloves. Put your safety gear on as soon as you step into your shop, and don't take it off until you're ready to leave. This way, you won't forget to put on an important piece of equipment.
In addition to gloves and goggles, you'll want a form of hearing protection. Power tools can be quite loud, and you don't want to damage your hearing while you work. It's also a good idea to wear a facemask, a respirator, or a face shield while you work. This will protect your face from debris, and will keep you from breathing in anything you shouldn't.
It's also important to dress appropriately for the shop. Make sure your clothing doesn't fit too loosely. If it does, it could become tangled in a tool. Take off any jewelry, such as neck chains, before you start working. Simple, comfortable clothing that's not overly loose is ideal.
While many people like to relax with a beer while enjoying their hobbies, it's best to avoid beer or any kind of alcohol in the workshop. You may think that a single drink is harmless, but you need your senses to be at their sharpest. It's best to be sober when working with power tools.
While it's a no-brainer that sharp tools are dangerous, dull tools are actually a bigger hazard. A tool that's too dull may bind or cause kickback. Make sure your blades and your bits are always sharp, and switch them out if they start to get dull.
If you need to swap out the blade or a bit on a power tool, make sure it's first disconnected from electrical power. Even if the switch it set to off, the tool could get bumped back on, which could cause a disastrous accident. You need to make sure there's no way a tool can come on before you start handling blades.
In fact, you may want to use a single extension cord for every tool in your shop. This forces you to switch the cord to a new tool every time you start working with something else, which ensures nothing is left accidentally plugged in. It'll also make you more aware of what tools are plugged in.
Before you start cutting a piece of wood, check it for nails or bits of metal. This is especially important if you're using a leftover piece of wood. If your saw connects with a nail, it can cause kickback, which can cause injury. You may want to purchase a metal detector so that you can check the wood before cutting.
When you do begin the cutting process, make sure to work against the cutter rather than with the cutter. Power tools are designed for wood to move in the opposite direction of the cutting head direction. If you cut with the wood, it'll be more difficult for you to complete a job, and it'll be easier for you to incur injury.
When you need to reach something in your shop, never reach over a saw blade. Just as with power tools, even a tool that's turned off can be bumped back on. Take the time to move around the blade. If you need to move debris that's directly against a blade, do it with a piece of scrap.
Make sure you turn your tools off if you're going to be distracted. Power tools require your undivided attention, and every distraction can put you in danger. If someone needs to talk to you or ask you a question, shut down your project and stop working until the conversation has been completed.
As long as you follow the basic safety precautions, it'll be easy for you to avoid injury in your workshop. Most people who are hurt while woodworking make the same basic mistakes. Take the time to protect yourself, and your woodworking experiences will be far more positive.
How to Select the Right Lumber for a Project
Have you ever wondered what people are looking for when they examine a piece of wood stock? Do you want to know how to select the best possible wood for your projects? Finding the right wood is important, and can make a woodworking project go much more smoothly.
When people examine a piece of wood, they're typically searching for defects. At times, a defect can make a piece of wood less suitable for a certain project. However, there are a number of other things you'll need to consider, for instance what type of wood would be best for your project, and how easy that wood will be to cut.
When you examine a piece of lumber, take a look at each of the stock's sides. See if you can spot any obvious defects. A defect in the wrong place can cause problems during a woodworking project. Once you learn how to spot a defect, it'll be easy to find them.
With that said, defects aren't always going to be problematic. Defects can be caused by a number of things, from knots to lightning strikes to insects to growth issues. Some of those defects can actually improve the appearance of your finished piece.
For example, defects in pine stock can often give a piece a very appealing appearance. The defects only add to the early, natural look of the pine. Think about what kind of look you want for your project before ruling out any and all pieces with defects.
After scanning for defects, you'll want to see if the wood has a bow. To do this, take the piece out of a stack, and then place one end on the ground. Move to the opposite end of the piece, and lift it enough so that you're able to gaze down its long axis.
From there, take a look at each of the board's edges. The board should be fairly straight in appearance. If there's any curving on the stock, that is called a bow. While a piece with one bow may still be usable, any pieces with multiple bows should be avoided.
Another thing you'll want to keep an eye out for is twisting on the length of the piece. This type of warping is especially difficult to work with, and is best to avoid for all types of projects.
You'll want to keep an eye out for something called a crook. Crooks, a type of defect caused by tree growth, should be avoided. However, if you're not going to be using the entire piece, stock with a crook may be acceptable. Check to see if you'll be able to cut in a way that bypasses the crook.
If you don't see any kinds of bows or twists, check the wood for cupping. This is a kind of warping that involves a curve along the board's width. Although it's possible to reduce cupping with the right tools, it's typically caused because of a problem with the wood. It's best to pass on a piece with cupping.
You'll frequently see cupping on one-inch thick pieces of stock. The easiest way to spot cupping is by checking out the stock's end grain. Even if you don't see any cupping, curving end grain is a sign that the wood will cup in the future.
After this, you'll need to examine the board's ends. There's a chance that you'll find small cracks on the stocks where the wood fibers are beginning to separate. Be very cautious about purchasing wood with these cracks. There's a good chance they'll grow into larger cracks in the future.
You should also make sure that the stock you buy isn't overly moist. At times, stock can change as it dries, causing cracks or other defects to occur. If you're not sure about how dry the piece is then you can examine it with a portable moisture indication meter.
Another option is to talk to employees about how long they've had that stock in house. Sometimes, newer stock hasn't yet had time to adjust to the climate in the area. It's better to buy wood that's slightly older so that it has time to acclimate.
In addition to checking your wood for defects, you'll want to determine whether it's the right type of wood for your project. The wrong wood can make a project far more challenging than it would be otherwise. Luckily, it's fairly simple to determine what kind of wood you need.
The first thing you'll need to determine is whether you want a hardwood or a softwood. Hardwoods, which include oak, cherry, and mahogany, don't dent or scratch easily. They are ideal for projects that require durability. Hardwood is what tends to be used for most woodworking projects.
As the name suggests, softwood tends to be fairly soft. Types of softwoods include pine, cedar and fir. While these woods aren't the best for projects that require durability, they work very well for basic construction projects and for simple furniture.
You'll also want to make sure your wood is the appropriate grade. Woods are graded according to the FAS, or "First and Seconds" standard. The higher quality the project, the higher quality grade you'll want. For hardwoods, the highest grade is FAS, and the lowest grade is No. 3B Common.
With softwoods, things are a bit simpler. There are really only two types of softwood: construction grade and re-manufacture. Re-manufacture wood tends to be very low in quality, and should only be used in projects where the quality of the wood doesn't matter. This type of wood is great for experimentation.
There are also unique advantages that certain types of woods offer. For example, teak has natural protective oils, which makes it great for outdoor furniture. Poplar is ideal for pieces with intricate woodcarvings. Each type of wood has its own benefits and disadvantages.
Take the time to learn more about wood so that you can always select the right type for your project. Finding the right wood can be challenging at first, but as you grow more familiar with the process, you'll find it gets far easier.
Making Cutting Boards
When you're a beginning woodworker, you'll need a few simple projects to start with. There's nothing simpler than a cutting board. This basic project can be done with pieces of scrap wood, which allows you to get comfortable with your tools without wasting valuable materials.
The ideal type of wood to use for a project like this is maple or birch. It's best not to use open-grained woods, like oak, for cutting boards as food can get embedded in the grain. Get a few solid pieces of scrap wood, and you can get started.
What You Need:
-
Circular saw or table saw
-
Untreated wood
-
Tape measure
-
Medium grit sandpaper
-
Pencil
-
Mineral oil
Start by using your pencil to draw the shape you'd like for your cutting board onto the wood. If you're using a circular saw rather than a table saw, make sure your design has a straight edge. If you're using a softer wood, it's also possible to make a cutting board with a jigsaw.
Use your saw to carefully cut out the design. Make sure you've read your saw's manual beforehand so that you can properly follow all safety instructions. When you've completed cutting your board, use the sandpaper to sand down the edges.
Take a clean cloth and wipe any and all dust off your board. Take a new cloth and begin to apply the mineral oil, wiping it on in the direction of the wood grain. Once you've finished a coat, allow it to dry according to the time suggested on the bottle.
From there, you'll want to add another two to three coats of oil. The oil is what makes the cutting board safe for kitchen use, so you want to make sure you apply enough. As before, allow a coat to dry before adding a new one.
There are a few things you'll want to keep in mind after a board is completed. First, you should make sure that you never run your board through a dishwasher or submerge it in soapy water. That could wash off the oil coating. In addition, you'll want to apply a fresh new coat of mineral oil every three to six months or so.
That's all it takes to make your own cutting board. This can be made with any scrap piece of wood, and it's incredibly easy. It's a great way to become more familiar with a saw, and a very good way to make gifts for family members and friends. Everyone can use a cutting board!
How to Make a Key Chain
Wooden key chains are another very simple project that's ideal for beginners. Because key chains are so small, even a little scrap of wood will work well. In fact, when it comes to this project, the smaller the better.
Because this project involves carving a pattern, you may want to use a type of wood that's well suited for carving, such as basswood or butternut. Both of these woods take detail very well. However, any type of wood can be carved, and you can use whatever type of wood you'd like for this project.
What you'll need:
-
Utility knife
-
A small piece of wood
-
Sandpaper
-
Stylus
-
Carbon paper
-
Drill bit
-
Varnish
Take your small piece of wood and work to carve it into the shape you desire with your utility knife. It's best to keep it simple, as cutting with a utility knife can be a challenge. Once it's finished, sand it smooth and wipe it clean.
Print a design in an appropriate size on a piece of carbon paper. You may also want to simply write your name or initials on the paper. From there, place the carbon paper on the wood and trace it with your stylus. Be careful not to move the pattern until the tracing is complete. To keep the paper in place, you may want to attach it to the wood with masking tape.
After that, remove the paper and trace the outline of your pattern with your utility knife. This will help the cut of your pattern to look cleaner than it would otherwise. After that, cut the wood around the outline of the pattern using the shallow blade of your knife.
From there, you can stop, or you can continue to make cuts in order to add dimension to the pattern. Your choice depends on how intricate you want the pattern to be, and how much texture you'd like it to have. You may want to cut the corners off any sharp outlines so that the pattern has a smoother transition.
Take out your sandpaper again and sand your finished pattern, cleaning up your overall design. Your aim should be to give your carving a uniform appearance. Fine grit sandpaper is ideal for this type of task. Clean off the dust once you've finished.
Take a small drill bit and carefully press it into the wood in order to make a hole for your key chain. It's best to do this with just a bit rather than with a drill because the wood you're working with is so small. The power of the drill could damage it.
Once your key chain is complete, you can apply a varnish. This will protect it from the elements, and will also give it a more professional appearance. Apply the varnish using a small paintbrush so that you'll be able to put on a smooth coat.
Once the varnish has dried, sand your key chain again before applying the second coat. This will give the coat something to stick onto. After the varnish is applied, you'll have the choice of repeating the process once it dries or stopping. Most key chains won't need more than two coats of varnish.
From there, the only thing you'll need to do is place a jumpring in the hole you've made. You may also want to add a small piece of string, ribbon, or leather in order to give your key chain a little extra personality.
Making a key chain is an ideal project for someone who wants to start woodworking, but doesn't have the money for expensive tools. The tools required for this project are minimal, and it's very inexpensive to put together. It's also a great way to practice pattern carving.
If you have a few small pieces of wood you'd like to do something with, or if you'd just like to get some experience with a utility knife, give this project a try. It's simple, it's fun, and it'll leave you with a beautiful, professional quality key chain.
Making a Magazine Holder
If you subscribe to any magazines, you'll need a place to put them! While you can buy a basic magazine rack at the store, a magazine holder you've built yourself will be far more attractive, and will have a lot more personality. Making a magazine rack is a simple project, but is complex enough that it gives crafters a chance to test their skills.
The type of wood that's best for this project will depend on how you plan to finish the project. If you'd like to stain the wood, it's good to use a natural wood such as oak, pine, or a soft maple. If you'd like to paint the wood, plywood and fir are good options.
What you'll need:
-
Jigsaw or handsaw
-
Drill
-
Two pieces of wood, 11%u2033 x 22%u2033 each
-
Pencil
-
Ruler
-
Sandpaper
-
Wood stain or paint
Take your two pieces of wood. Using your pencil, draw a faint line down the center of each piece. Then, draw a second line across the middle. These lines will help you see where your two pieces of wood will cross.
From there, you'll want to cut out a line on the right and left half of your respective wood pieces. Use your pencil lines to determine where the lines should be cut. Make sure your cut doesn't go beyond the center point you have marked on your wood. If you cut too far, the pieces won't fit together properly.
Take your drill and drill out a hole right in the center of each piece. Make sure the hole fits within your pencil line boundary. After that, use your jigsaw or hand saw to cut out a piece on the side of the wood piece, cutting right up to the carved holes. Clean up the cuts with sandpaper, and wipe away the dust.
Check to make sure that the two pieces of wood slot together properly. If they don't, take your sandpaper and sand off a little more wood. Continue to sand and test until you're happy with the way the two pieces fit.
Wipe away the pencil line, and prepare to stain or paint your pieces. If you're going to stain, prepare your stain by stirring it well, and apply rubber gloves to protect your skin. Using a sponge or a paintbrush, apply a generous coat of the stain to the wood. Use smooth, continuous strokes so that the paint will be applied evenly.
Give the stain time to absorb. How long you let it set will depend on how dark you want the stain to be. The stain will get darker the longer you wait. It's best to wait at least five minutes, and you shouldn't wait any longer than 15 minutes. Remember that you can always add more stain, but it's difficult to take a stain off.
Once your stain is finished and dried, you may want to add a finish to protect the stain. This will keep your stain looking great in the future. Most people use a polyurethane finish, but there are other types of finishes available. Examine the options at your home improvement store before making your final choice.
If you want to paint your magazine rack, take the time to carefully sand it down first. Paint will adhere much better to a smooth surface. Once you have finished sanding, clean it thoroughly with a cloth. Paint won't properly adhere to a dirty surface. The cleaner your wood is, the easier the painting process will be.
Next, you'll want to apply a few coats of primer. Primer will help give your finished rack a uniform and professional quality look. Simply paint on the primer the same way you would apply an ordinary coat of paint. Use gray primer if you're planning on painting the rack a dark color, and white primer if you're going to go with a light color.
From there, you can start painting your wood. Make sure you fully load the paintbrush so that you can get good coverage on your wood. Use short, even strokes, reapplying paint as needed. Make sure you don't let the paint sit too long between coats. If you do, it'll be harder to apply additional coats evenly.
Once the paint is finished drying, you may want to apply a sealer or a topcoat. However, most paints sold today actually contain protectants that will allow you to skip this step. Since the magazine rack will be kept indoors, it's likely that an extra finishing coat won't be needed.
Whether you choose to paint or stain your rack, you'll be left with a beautiful handmade project. Best of all, it'll be something you can use regularly. Every time you see your magazine holder, you'll be able to admire your handiwork.
Building Simple Floating Shelves
Just about everyone could use a few more shelves to store or display items. Floating shelves are elegant and have a unique and interesting appearance. They're designed to look as though they have no support and are actually floating alongside the wall.
Floating shelves are one of the most useful projects that a beginner can properly tackle. They're also very versatile. Literally any type of wood can be used for this project. You can even re-purpose an old piece of furniture.
What you need:
-
Two identically sized pieces of wood
-
Two to three long strips of wood
-
Hand saw or table saw
-
Pencil
-
Wood glue
-
Nail gun
-
Paint or varnish
-
Shelf mount
To begin, you'll need two pieces of wood that are exactly the same size. If necessary, cut the wood with your hand saw or table saw to get them to the right size.
After that, take your long strips of wood and place them up against the sides and the back of each of your wood pieces. Mark where the wood ends with your pencil, and then cut the wood pieces to the appropriate size.
Apply wood glue to the strips, and attach three of them to one of the one of the wood panels. After that, use your nail gun to make sure the strips are completely secure. Once the glue has had time to set, apply wood glue to the attached strips, and place the second panel on top of it. Secure it using your nail gun.
If you desire, you can apply a coat of paint or a stain to the wood at this time. You'll also want to take the time to paint or stain the remaining long strips. Instructions on how to do that can be found in the previous chapter. If you do complete this step, wait for the stain or the paint to fully dry before continuing work on your shelf.
Measure both the length and the width of your shelf's hollow space. You don't need to measure the entire shelf. The hollow you've constructed is what you'll be using for your next step.
Cut another long, thin strip that matches the length of your hollow. This is what you'll be using for your wall mount. If desired, you can cut two additional strips that are as long as the hollow is deep, minus an inch. They need to be slightly shorter so that the shelf will sit properly against the wall.
Make sure your wall mount fits properly inside your hollow. If it doesn't, cut and sand it down as necessary. Once you've made sure it fits properly, you can move on to the next step.
Using your wood glue and your nail gun, attach the wall mount base to your two shorter strips. Put one on each side of the wall mount in order to create a u-like shape. After that, you can attach your shelf mount to your wall.
Carefully slide your shelf onto the attached mount. It should fit perfectly. You can allow it to rest on the mount, or you can give it a more secure fit using your wood glue. If you do this, the shelf will be permanently attached to the mount.
From there, you can repeat this process to make as many shelves as you desire. Remember that your shelves don't have to be the same dimension. In fact, floating shelves often look more visually interesting when they're not all the same size. Experiment, and make a series of shelves you love.
Floating shelves are surprisingly simple to make, and have a lot of usefulness. They can be a great fit for just about any room in the house. This is a project that gets easier to make the more you do it. Practice a little until you can make shelves like an old pro.
Crafting a Birdhouse
For many, a birdhouse is their first woodworking project. This project is especially popular with children, as they enjoy seeing their finished birdhouse afterwards. It's a great project to take on together as a family.
The birdhouse will need to be made from thick wood. At minimum, the wood used should be 3/4 inches thick. It should also be a type of wood that's well suited to the outdoors, like oak or teak. You want your birdhouse to last.
The birdhouse below is a basic design that will attract a wide range of birds. However, if you adjust the measurements, you'll be able to attract even more types of birds. A general rule of thumb is to consider the size of bird you want to attract when building your birdhouse. Smaller birds want smaller birdhouses, and larger birds want larger birdhouses.
What you need:
-
Table saw or hand saw
-
Wood
-
Drill
-
Hammer
-
Nails
-
Utility knife
-
Screwdriver
-
Screws
Start by cutting your wood into the appropriate sizes. If you start with a 1 x 6" board, you should be able to get all the pieces from a single board. You'll need four 5-1/2 by 10" pieces, one 5-1/2 by 7-3/4" piece, and one 5-1/2 by 5- 1/2" piece.
Using a 1/2" drill bit, drill a hole about 7" above the floor of one of the 5- 1/2 by 10" pieces. Carve a larger hole directly above that. Taking your screwdriver, scratch grooves on the interior side of the board. These grooves will make it easier for birds to get out of your birdhouse.
Drill a series of holes into another 5-1/2 by 10" piece and the 5-1/2 by 5-1/2" piece. These holes are for drainage and ventilation. They'll allow the birdhouse to function properly.
Next, it's time to nail all the pieces together. Use the 5-1/2 by 10" for the front piece and then use two more for the sides. Use the 5-1/2 by 10" with the ventilation holes as the roof. The 5-1/2 by 7-3/4" will be the back of your birdhouse, and the 5-1/2 by 5-1/2" piece with the drainage holes will be the bottom.
Start by attaching the back to the sides. Do this carefully; making sure each hole is straight. Next, using your utility knife, cut about a half inch off each corner of the floor. From there, you can nail it to the sides and back.
Finally, you'll want to attach the front and roof using screws. This is so you'll be able to unscrew these pieces of your birdhouse if you want to clean it in between seasons. Deck screws are ideal for a project like this, but you can use other types of screws if desired.
After this, you can paint your birdhouse if desired. Since this birdhouse will be used outdoors, you'll want to make sure that you apply some kind of sealer when the paint is finished. Otherwise, your paint is likely to fade or wash away over time.
That's all it takes to build a beautiful and functional birdhouse. It's a basic project that doesn't require much beyond the use of a few basic tools. This makes it a great choice for younger woodcrafters, and an excellent project for first-timers.
Building a Bench
One thing many woodworkers are interested in making is furniture. They want to create something they'll really be able to use day in and day out. Although making furniture often requires more tools and a bit of practice, there's one project that can be made very simply: a bench.
The instructions below are for a simple outdoor bench. A material like pine or oak would be ideal for this. However, as long as you're willing to seal the wood to protect it from the elements, you can use any type of wood you like.
What you need:
-
Circular saw or table saw
-
One 2 by 10" board
-
Two 8' long 2 by 2" boards
-
Two 8' long 1 by 4" boards
-
Two 8' long 2 by 4" boards
-
Screws
-
Screwdriver
Take the 2 by 10" board and cut it into two identically sized pieces using your circular saw or a table saw. Sand and wipe away the edges of the board if needed. These boards will be the side of the bench.
Next, you'll want to attach the long 2 by 2" boards to the sidepieces. Attach the boards 1-1/2 inches from the top, using an appropriately long screw. You should use two screws for each side of the bar.
Take the 1 by 4" boards and place them at the front and the back of the bench between the two sides. The top edge of each board should be flush with the top of the sidepieces. Attach them using long screws, using two screws for each end of the boards.
Your next step will be to add the seat of the bench. This will use your 2 by 4" boards. Place them so that they spill slightly over the front, back, and sides of the base of your bench. There should be a slight space between the two boards.
Take your long screws and attach the seat to the rest of your bench, going through the top so that the screws enter the sideboards. Three screws should be used for each side of the board, so there will be six screws for each board in total. More screws can be added if desired.
Depending on what you'd like to use your bench for, you may want to add some cushioned seating. You can either make your own cushion, or purchase outdoor seating cushions at your local home improvement store. The simplest way to attach them to your bench is with Velcro.
Attach the rough, scratchy side of the Velcro to your bench, and the soft, fluffy side to your cushions. Your cushions will be washed, and you'll want a type of Velcro that will work well for that. The best way to attach the Velcro depends on the type of cushions you choose. Experiment with cushion layout before placing the cushion on the bench.
You may also want to paint your bench. As mentioned above, some kind of outdoor sealant will be necessary. Even if your bench is on a covered patio, the constant exposure to the elements will cause damage over time. To avoid frequent touch-ups, properly prime and seal your bench before painting.
That's all you need to do to make a simple, yet beautiful outdoor bench. This is an incredibly easy furniture project, but the finished product is quite impressive. A bench is a great way to show your friends and family member just how much your woodworking skills have developed.
Where to Store Your Extra Wood
After you finish a woodworking project, it's likely that you'll have some extra pieces of wood left. You may think that you can leave this wood in your workshop and call it a day, but that isn't necessarily true.
Wood is a material that adapts to its surrounding environment. Wood will shrink or expand depending on the moisture level of the air. Because many workshops are located in areas that tend to be moister, like a basement or an outdoor shed, it's likely that this will affect the wood you use in some way.
In addition, wood stored the wrong way can warp or bend over time. When wood is left standing, it will eventually begin to sag between its standards. This can cause twisting or other forms of warping, and can make your wood far more difficult to deal with.
Ideally, you'll want to store your lumber in a place where it won't be exposed to extreme moisture or dryness. However, this isn't always possible. Most people have limited space, and they may not have a place to keep lumber outside of their main house.
However, if you're willing to have lumber in your house for a short period of time, wood can usually recover from moisture damage. Before you start a project, bring the wood you're going to use into a different part of the house and let it acclimate to the temperatures there. It should return to its normal size, allowing you to use it for its intended purpose.
However, this can be a frustrating solution, and it doesn't solve the issue of warping or bending. To avoid this, you may want to construct some kind of shelving for your extra lumber. Once you've tackled some of the projects in this book, putting up a few simple shelves should be a breeze.
There are two benefits to storing your wood on shelves. The first is that it will allow the wood to lay flat. When wood is flat, it will be less likely to experience warping, and it will be less likely to experience any dramatic changes in size.
The second benefit is that it can slightly reduce the amount of moisture your wood is exposed to. The floor tends to be the dampest part of a shed or basement. Getting your lumber off the floor and onto a shelf can help avoid a great deal of problems.
If you don't have any way to store your lumber indoors, you'll need to come up with an outdoor storage solution. Find a way to keep your lumber off the ground. The simplest solution would be to place it on a basic wood pallet. From there, you'll want to stack your lumber flat.
After that, cover the lumber with either tarp or plastic. Check on it periodically. It's common for bugs and insects to move to areas like these, and you want to make sure they don't make a home in your lumber. They could cause significant damage to the wood.
While most wood can be stored outdoors for an extended period of time, there are some types of wood that handle the outdoors poorly. For example, pine will turn gray after extended exposure to the elements. If you have to store pine, make sure you bring it indoors and use it before too long.
When you do bring your wood back inside to use, give it some time to adjust to the new climate first. Lay your wood flat, and help it to dry out more quickly using a box fan. While your wood may have sustained some damage outside, in time, it should be close to the condition it was in when you bought it.
Wood can be expensive, and it's important to take care of any extra wood you do have. Whether you build shelving or use an outdoor storage solution, you'll want to make sure that your lumber remains in the same condition it was in when you bought it.
Dealing With Common Woodworking Problems
When you spend a lot of time woodworking, there are some issues you may eventually run into. Despite your best efforts, there may be issues with your wood or your other materials that will need to be addressed. Thankfully, most of these problems have very simple solutions.
Fixing a Stripped Screw Hole
Sometimes, the screw hole of one of your projects will be stripped out, leaving it unable to support the fixture it was originally designed to hold. This is a frustrating issue, but there are a number of simple solutions.
The easiest fix is to use a larger screw. Sometimes, a slightly bigger screw is all you need. If this isn't a viable solution, there are still other options available.
If the wood you're working with is a softwood, you may be able to fill in the hole with strips from the same type of wood. Cut off a few thin shavings, dip them in wood glue, and place them into the hole until it's filled. Allow the glue to dry, then trim and sand away the excess. Tap a slight hole into your fill, and then place the screw back in through the new opening.
A similar fix will work for hardwoods. However, you'll need to be more careful about the wood you use for your fill. It will need to be as close to the wood you're repairing as possible.
You can also try fixing the hole with epoxy or similar substances. However, this should be used as a last resort, as chemical substances can cause damage to your wood.
Wood Odors
One of the most common problems woodworkers will experience is an odor in their wood. Wood can absorb scents from their environment, and it can often take on a strange smell. This smell can make it hard to use the wood for its intended purpose.
There are a number of ways to remove an odor from a piece of wood. One simple way is to make a natural cleaner by mixing one part olive oil to 24 parts white vinegar. Place the finished mixture in a spray bottle, and shake the bottle thoroughly. Spray the mixture onto the wood until the smell has vanished.
Another odor removal method involves kitty litter and baking soda. Both of these things are natural odor removers, and the combination of the two can make most odors fade away. Make a paste combining baking soda, water, and a small amount of kitty litter. Apply it to the wood, avoiding any end grains and joints. Let it sit for a few hours before wiping it clean.
If the odor persists, you may need to turn to commercial cleaners. Cleaners designed to get rid of pet odors can be a very good way to get a bad smell out of wood. Spray the cleaner onto the wood, and then wipe it off afterwards with a damp cloth. Repeat the process until the odor is gone.
Glue Run-Out
If you frequently work with glue, there's a good chance you'll experience glue run-out. This can be a big problem, especially if you plan to apply a finish to the wood. When glue runs out onto the wood, it will fill any exposed pores, which will keep the finish from seeping in to that part of the wood. Even if the glue stain isn't visible before the finish is applied, it'll be visible afterwards.
Thankfully, there's an easy solution to this. Before applying your glue, take some masking tape or painter's tape and apply it to all the surfaces adjacent to the joint. That way, if some extra glue does squeeze out, it'll wind up on the tape and won't wind up seeping into the joint.
Dealing With Damaged Wood
Even if you thoroughly check for damage and defects when you buy your wood, it's possible that it will become damaged over time. Natural wood is an imperfect material, and it can be greatly affected by its surroundings.
However, while undamaged wood is ideal, most types of damage can be easily addressed. For example, small blemishes such as holes can easily be filled with wood fillers or putties. All you need to do is apply the substance to the hole, let it dry, and then sand it smooth.
However, these fillers can only solve a small problem. If you find a big crack, you'll need a bigger solution. The best thing to do is to pour polyester resin over the cracked areas. It will bond with the wood and fill in any cracks. To ensure the resin stays within the crack, tape up exit points with masking tape or painter's tape.
Polyester resin will change the color of the wood, but it'll also fill in your crack, allowing you to use this wood for future projects. This solution is best for wood that will be painted a dark color, or wood that will be in a place that won't be seen.
It's likely that most woodworkers will run into one or more of these problems over time. Thankfully, the solutions are very easy. As long as you know how to handle common problems, you'll never have to worry about a little issue turning into a disaster.
Conclusion
The history of woodworking is long and fascinating. In ancient times, wood was one of the very first materials that early humans worked with. Society was able to grow and develop because of the woodworking skills that humanity built.
You can see signs of this rich history everywhere you look. Ancient Egyptian drawings illustrate people working with wood, and sketches of woodworking shops can be dated back to the medieval period. Throughout time, all across history, you can see the myriad ways that woodworking has helped the world grow.
Over time, the way we've worked with wood has changed dramatically. More efficient ones replaced the simple, crude stone tools our ancestors used, and the modern tools we use in the present day eventually replaced many of those. Today's woodworkers have a wealth of options at their disposal.
But while access to more powerful tools has made woodworking more accessible, it hasn't changed its core benefits. Woodworking is a skill that enhances the life of both the person working with the wood, and the lives of the people who get to enjoy the products they make.
While any new woodworker will have to start with simple projects, they'll be able to construct far more impressive items as they gain additional experience. The more time someone spends woodworking, the more beneficial this skill will be.
You may be starting out with cutting boards and birdhouses, but you'll eventually be able to make things like a bed or a set of patio furniture. You could even construct a shed that could become your new workshop. Wood is an incredibly versatile material, and the possibilities it offers are nearly endless.
When someone is new to woodworking, it may seem intimidating. The prices of power tools can give anyone sticker stock, and learning how to work with these tools can take time. Even the most basic of projects will require a lot of effort if you don't have experience with the tools.
But over time, those skills will blossom. If you're willing to put in the time and effort, you'll be able to craft complex items with ease. Before long, you'll no longer need to look at instructions when you want to construct a project. You'll be able to come up with projects of your own.
It will also get easier for you to select the right materials for a project. You'll be able to spot damaged wood in an instant, and will develop a strong understanding of what types of wood are best for various projects. You'll learn how to re-purpose old wood pieces, and how to work around any issues that you find.
You'll be able to handle problems, come up with storage solutions, and will figure out ways to make projects better. You'll learn the best ways to store materials, and will figure out how you can use the materials you have in a more efficient way. The number of ways in which you'll grow are endless.
Throughout all of this, it's important that you make safety a priority. Although woodworking is extremely rewarding, it can be very harmful if you're not willing to play it safe. Injuries incurred while woodworking can be devastating, and can cause lifelong disabilities or even death. Wearing safety gear may be slightly inconvenient, but the protection you receive from potential risks make it more than worth it.
As long as you never forget the importance of safety, your journey into the world of woodworking will be an incredible one. You'll be amazed at what you'll be able to accomplish in even a few months from now. If you're willing to put in the effort, you'll be able to grow your abilities at a tremendous rate.
You may be a beginning woodworker now, but before long, you'll be a seasoned pro. Soon, you'll be marveling at the things you can make from wood, and you'll have an even deeper appreciation for your newly found hobby.